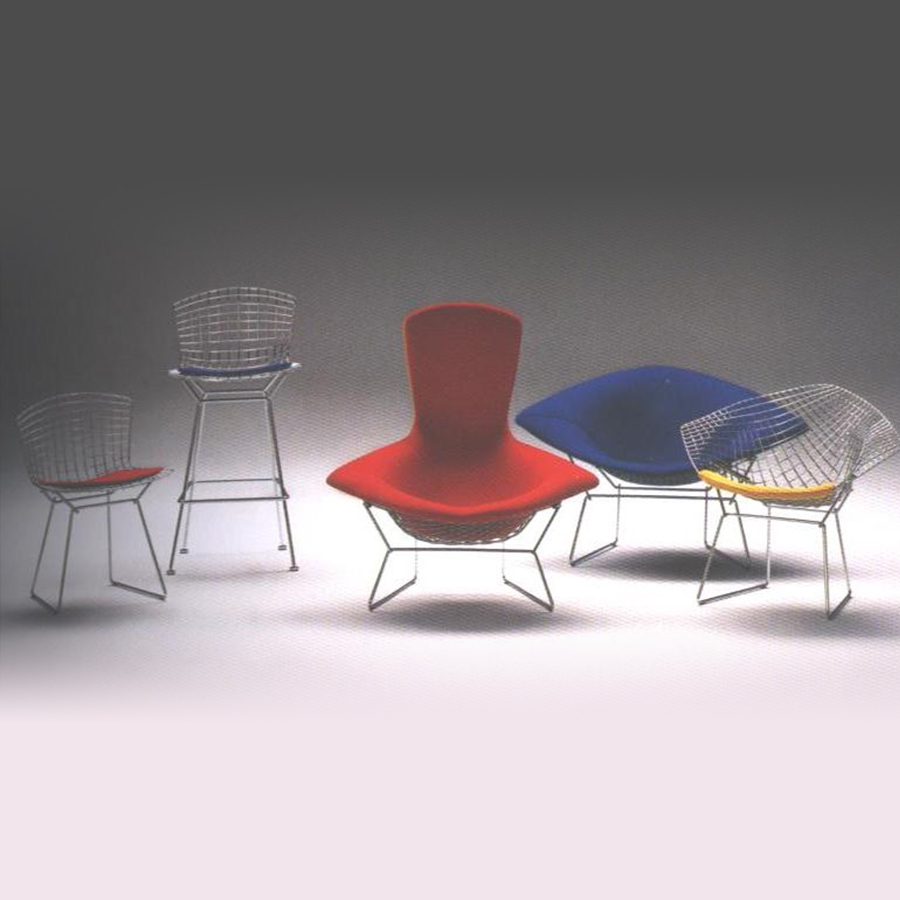
Because the majority of public questions refer to Bertoia chairs, allow us to give a brief background on the furniture before getting to other topics. If your interest is elsewhere, skip ahead.
Knoll International produced the first Bertoia chairs in 1952 and has kept the iconic collection in continuous production under the merged MillerKnoll brand. The Diamond Chair was first displayed in 1952 and actually in production by 1953. The side chair, bird chair, bar stool and wide diamond were all released in the early 1950s. The Children’s chair debuted in 1955 but is now available only in Europe. The gold-plated Diamond chair was released in honor of Bertoia’s centennial in 2015. The Asymmetric Chaise, although designed and prototyped in 1952, was not brought to mass production until 2005.
In late 1952, Harry had completed the designs as well as the initial jigs and was eager to turn his attention to sculpture. The parting was pleasant, and Knoll gave him extra funds to acquire the chair rights forevermore. This bonus allowed Bertoia to initiate the purchase of the Pennsylvania farmhouse in which he stayed until his death in 1978, and to transition to sculpture, his true passion.
Numerous European countries, with the guidance of Knoll, acquired their own patents and commenced production of the Bertoia chairs. Each country had slightly different connectors and details. East Greenville, Pennsylvania, remained the main US production location for decades. In 1986, all Bertoia chair production was shifted to Verona, Italy. At that time, the wire diameter increased, the waterfall edge was added and the connectors were changed. The “Knoll” stamp was added in 2004. Further questions are answered below.
Frequenty Asked Questions
Our most common frequently asked questions revolve around the Bertoia chairs, thus we give a bit of background here first. The rest of the questions are below.
Background:
Harry Bertoia (1915-1978) moved to Pennsylvania from California to work for Knoll in 1950. Knoll is the manufacturer and copyright holder of all Bertoia chairs. Chairs, based on steel grid wire forms, were designed by Harry Bertoia between 1950 and 1951 and further developed for production by Harry and the development team consisting of Richard Schultz, Don Pettit and Bob Savage in 1951 – 1952. They were first introduced in December 1952, and have enjoyed steady continuous production since 1953. To state the obvious, nearly all products that have been in production for over 63 years undergo evolutionary changes over time. Most are a response to field failures, structural improvement or cost reduction. Others are a response to external forces.
For the sake of discussion, one can consider all Knoll Bertoia chairs as being either early style (1986 and earlier) or late style (1986 and later). Prior to 1986, all Bertoia chairs were manufactured in East Greenville, Pennsylvania, or overseas by Knoll subsidiaries or under license. At various times, Bertoia chairs were manufactured in Argentina, Belgium, Finland, France, Germany, Italy, Japan, Sweden and Switzerland. All chairs of pre-’86 manufacture are very similar and are often only distinguishable by the wire diameters used (close metric diameter equivalent to US standard wire gauges.) See Photo 1 with yellow tags. It must be noted that, since foreign-made Bertoia chairs were never imported to the US, that it is very unlikely to encounter them here in the US.
All chairs made before 1986 are characterized by lightness and transparency. Harry liked to think of his chairs as being “mainly made of air.” That changed when the manufacture of the entire Bertoia line was shifted to Italy. At that time, the collection was retooled and major changes were made. Most obvious was the significant increase in wire diameter used throughout which changed the character of the chairs from transparency to form. See Photo 2.
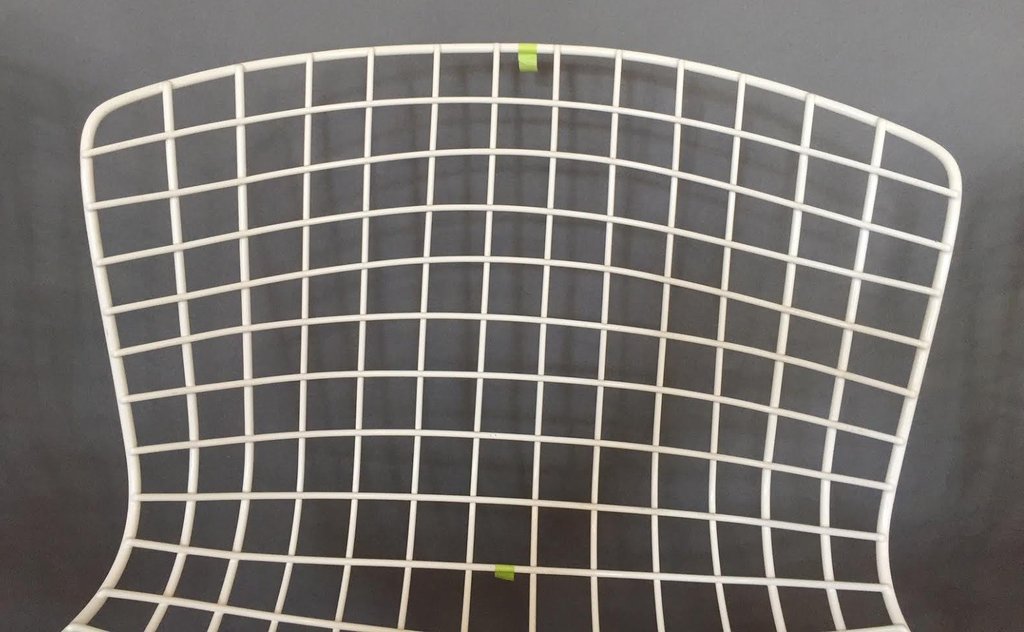
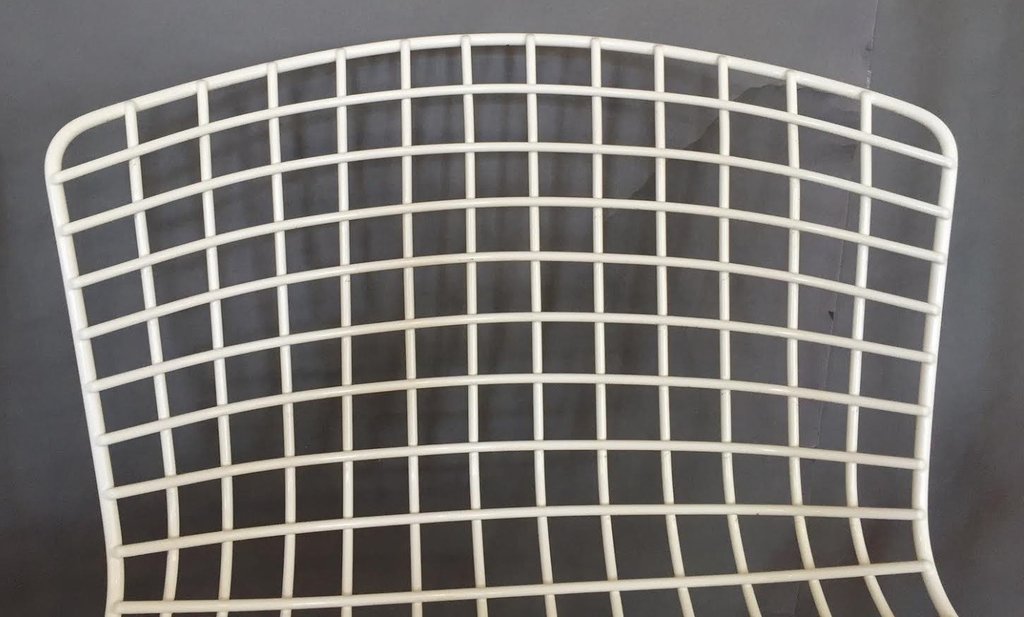
Other changes include altering the seat-back angle, the addition of a “waterfall” at the front edge and the use of the “paperclip-type” base connectors.
Many other minor changes have taken place over the years. Most of the comments below are specific to the 420 Side Chair but apply to other models as well. These include:
- GLIDES – Various glides have been used over the years… or no glides at all. The first ones were extrusions that snapped on (and unfortunately snapped off). Later ones are injection-molded with an integral pin that is driven into a blind hole on the bottom of the base.
- “KNOLL” STAMP – In 2004, Knoll began to discreetly stamp the word “Knoll” on the upper part of the base.
- UPHOLSTERY – All chairs are available with or without upholstery, either in the form of a seat pad or fully upholstered.
- LINE ADDITIONS – During the 1950s and 60s, a number of additions were made to the original scope. These included the 427 fiberglass version of the 420 shell, the 425 (child-size 420 chair), the 426 (baby-size version of the 425, and the 428 barstool (in two heights). During the 2000s, two more designs were added. The Asymmetric Chaise, which was part of the original scope but never produced, was finally put into production in 2005. In addition, a new scaled-down child’s version of the 421 small diamond chair (never part of the original scope) was also introduced. Finally, an injection-molded polypropylene version of the long discontinued 427 shell (side chair) was reintroduced in 2016.
Tips for recognizing authentic Knoll chairs
Despite the evolutionary and more revolutionary changes (newer Italian production) that have taken place over the years, it’s surprisingly easy to spot the originals. While the comments below are specific to the 420 side chair, they generally apply to the others as well. We look at two places which 99% of the time positively identify genuine Knoll chairs from the knock-offs.
First is the upper back. On the Knoll chairs, the top basket wire is a fair curve that mimics the curvature of the top of rim wire. The top corners are perhaps the most critical clue. The corner radius is neither too “soft” nor too “tight” (compare to above photos of Knoll chairs for a reference). Also, the “cell” described by the basket wires (both horizontal and vertical) and the rim wire at the top corner is horizontal in character (very unlike nearly all knock-offs).
Second is the base. The inside bend radius is very tight on all Knoll chairs. A 1/2” diameter dowel should nest neatly on the inside of any base bend (knock-offs have a much more generous bend radius.)
Another detail on the Knoll chairs is that the grid wires are cut at an angle (some knock-offs have a straight blunt cut of the grid wires). See Photo 3.
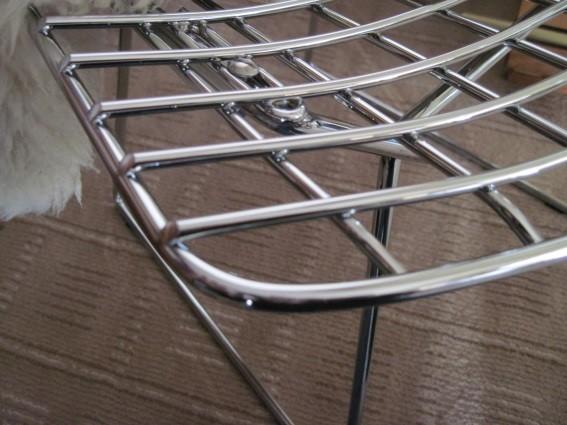
Tips for identifying a knock-off
It’s truly amazing that any company choosing to knock off an iconic product such as the Bertoia collection should be so sloppy in detail and make so many changes that scream knockoff! But such is the case.
Descriptive words such as “Bertoia style,” “in the manner of Bertoia,” “inspired by Bertoia,” or “Bertoia reproduction” are a sure tip-off that it’s a copy. If the word “Knoll” is mentioned, it is still no guarantee as to its authenticity.
Many manufacturers of knock-offs utilize a “double rim-wire.” While the double rim-wire was used for small number of 420 production chairs in early 1953, they were quickly replaced with a single larger diameter rim-wire. Very few double rim chairs were shipped to customers. Note that a double wire rim has always been used on the ottoman and asymmetric lounge and a partial double-rim has always been used on the 423 “Bird chair.” Every new double-rim side chair is a knock-off.
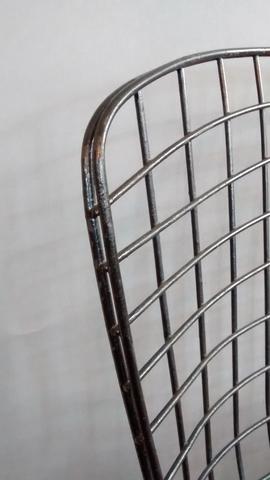
original, rarely found today.
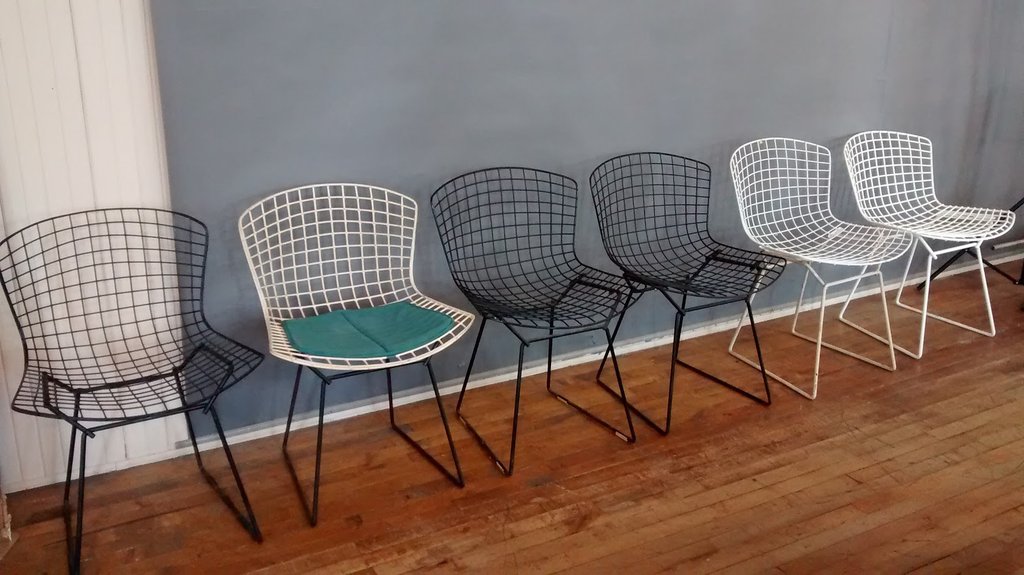
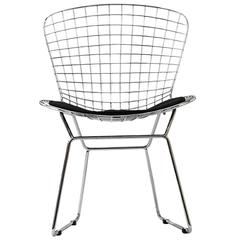
overlap and an overly generous corner radius;
all sure signs of a current knock off.
A few other notes
Eames vs. Bertoia There seems to be some confusion on the Eames wire chair vs. the Bertoia wire chairs. Harry Bertoia worked with Charles Eames in the late 1940’s and was toying with, and making drawings of, the wire grid concepts. Eames carried this idea to fruition. Below is the Eames wire chair first produced by Herman Miller in 1950. The Bertoia chairs have a similar same wire grid concept but came out in 1952.
Why is authenticity important? Why is it important to get an authentic designer chair? Why not get a reproduction that looks roughly similar and costs half the price? There are several reasons to get the real deal when it comes to designer furniture. First of all, by purchasing from the authorized manufacturer you are honoring the designer and getting a piece of his energy. He (Harry Bertoia or any designer) was an artist and had specific intentions for his design. The authentics are faithful to the designer’s original vision, while knock offs are not. Secondly, you will get a quality product with customer service behind it if you buy the authorized models. We’ve heard horror stories of offices or homeowners buying the cheap versions and being disappointed in the durability and comfort of their purchases. Welds fail and the chairs are simply not comfortable. And finally, an authentic designer purchase will hold its value much better than a knock-off. One Knoll chair is always more desirable than many China-made or European copies. Would you rather have one Picasso or twenty photocopies of a Picasso?
KNOLL or HarryBertoia Foundation? If there are questions about chair care, photos rights, replacement parts, manufacturing or prices, please contact your nearest Knoll representative (knoll.com). The HarryBertoia foundation (harrybertoia.org) can help with history, timeline, design aspects, Harry’s philosophy and non-material questions. For assistance on authentication of rare or unusual Bertoia chairs, contact the foundation and we will direct you to our expert Bill Shea. A fairly comprehensive chair history can be found in Celia Bertoia’s book, The Life and Work of Harry Bertoia, 2015, Schiffer. An even more extensive history of Bertoia chairs is being compiled by Bill Shea right now.
We hope these pointers will help you in your search for authentic Bertoia chairs.
Bill Shea, formerly Senior Industrial Designer for Knoll Product Development, recently retired from his own design, development and engineering consultancy, Shea+Latone, Inc. Celia Bertoia is the Director of the HarryBertoia Foundation and author of The Life and Work of Harry Bertoia.
Authentic chairs have an overlap of frame rods over leg rods. They do NOT have a double wire rim. There is much more. See details above.
You can also listen to this podcast or view the extensive YouTube video.
We do NOT authenticate chairs. See above.
Look for a Design Within Reach in your area https://www.dwr.com/stores?lang=en_US or find your Miller Knoll showroom location here: https://www.millerknoll.com/where-to-buy/find-a-showroom
PRELIMINARY INSPECTION
Any household product in service for up to sixty years is going to show signs of wear and tear and that includes the robust steel wire Bertoia chairs that have been in continuous production worldwide since the first customer order shipments in 1953. If upholstered, the cushions fade, wear and generally look sad over time. Cosmetically, the basket and base can fade, chalk, chip or rust and structurally, wires can break and welds fail. So the first step is to assess the damage which will determine what corrective action(s) should be taken. This could entail anything from minor touch-up to a major project.
UPHOLSTERY
This is the easy one. Different upholstery options were offered at any given time – typically: no upholstery, a simple seat pad, two-piece seat and back pads and fully upholstered. Also different fabrics and upholstery details have been offered over the years. But, the good news is that replacement upholstery cushions are very much available directly from Knoll and lower priced knock-off replacements are available online. Knock-off quality varies so be careful… you get what you pay for. Note from Celia: I’ve had local upholstery shops do a very good job on full upholstery with cost dependent on fabric; talk to your local shops. A Diamond, Bird and Ottoman total came to $500 here in St George, Utah.
FINISH
During its production history, the finish has changed many times and perhaps the most difficult task in refurbishing the finish is determining what the finish is! Many have been used over the years and the ‘technical descriptions’ in the price lists can be vague, confusing or downright wrong.
Early chairs made from 1953 – 1976 were only available in black, white and chrome or black and white two-tone (chrome was added in 1956). The black was a simple black oxide finish and was used through the mid ‘60s (this is the same finish used for black nuts and bolts found in the hardware store). This proved to not be a very durable finish and prone to rust so later ones were also dipped in cosmolene and wiped off. In the early ‘70s the catalog description was changed to ‘black epoxy’ which I presume was powder-coated.
White – White was described in a head-spinning number of ways from white vinyl, lacquer, white fused, white epoxy and Rilsan (nylon). The different finishes were applied in various ways but the most common one was (and is still used to this day) is applied by a process known as ‘Fluidized Bed’. This produces a very heavy build, perfect finish and was/is used for epoxy and Rilsan (nylon). It’s interesting to note that the Rilsan (nylon) powder which was developed in Italy in the early ‘40s is derived entirely from castor beans and therefore a ‘green’ material. It’s also the most common finish found on white Bertoia chairs.
Colors – Red, yellow, green, blue, brown (plus white and black) polyester or epoxy powders were added to the scope in the 77/78 price list. These were applied by powder-coating.
Plated – Polished chrome has been a standard option since 1956. Satin chrome and gold-plated finishes have been added in recent years.
Though its not clear if any were shipped to customers, one still finds chairs with a white very gloppy, saggy (frankly, ugly) finish usually referred to as the ‘dish drainer’ finish which is just that: the dip-molded finish used on Rubbermaid dish drainers.
By now you’re probably scratching your head wondering what kind of finish is on your white chair. The good news is that it really doesn’t matter… regardless of color. Let’s take a close look at your chair and determine the best corrective action.
Cleaning – It’s about time. If you hadn’t bathed in decades, you’d need a good cleaning, too. Begin with a bucket of hot water and dishwashing liquid (I recommend Dawn detergent) and a medium-stiff dishwashing brush. If that’s not sufficient, move up to dishwasherliquid which is more alkaline. Rinse well and allow to dry thoroughly.
Minor Dings – Chips, scratches and scrapes can usually be touched-up with reasonable success. Begin by scraping or sanding to remove rust. Be sure to keep the sanded area small and blend to a feather edge with the surface of the paint. Clean with alcohol and you’re ready.
Some recommend the use of product called ReRack or Uber Goop, available online or at many hardware stores. This is intended for the repair of dishwasher racks and is only available in white or gray color. Even shaken, it’s lumpy and difficult to apply neatly. The resulting patch is much too soft and rubbery to my liking. I don’t recommend it.
I find a much better alternative to be automotive touch-up paint such as Dupli-Color Scratch Fix. It has an applicator pen and brush and is easy to apply. Don’t forget that it shrinks quite a bit when dry, so it may need two coats. Also, be careful in the color selection as there are a number of whites to choose from and some will match your chair better than others.
Major Issues – Rust, flaking, chipping and peeling are not uncommon, especially on chairs that have been used outdoors for extended periods of time. This requires fully stripping and refinishing. Also, if you find structural issues such as broken wires, failed welds et cetera, stripping is a must.
The stripping process is complicated and chemical strippers rarely work. Usually the finish is baked off in a large oven at around 700 degrees F and then lightly sandblasted. Finally, the base and basket are repainted using either the powder-coat or fluidized bed method. Because powder-coaters are to be found nearly anywhere whereas fluidized bed contractors are few and far between, powder-coaters are probably your only practical choice. A good powder-coater should have numerous powder options: colors, gloss level, high-build, UV-stabilized and so on. Some are more appropriate than others so you should discuss which is the best choice for your application. The good news is that most powder-coaters offer one stop shopping: stripping, bead-blasting and painting in-house. The cost should be around $100 – $125.
STRUCTURAL REPAIR
Anything can break but not everything can be repaired. Fortunately, Bertoia chairs usually can be. Just keep in mind that all repairs require that the chair be stripped first.
Broken Welds – The most common structural problem is broken welds, especially on chairs made in the early ‘50s. Keep in mind that all Bertoia production chairs were welded (more accurately, resistance welded) as opposed to brazed, hard soldered etc. but repairs are best made by brazing, or better yet, silver soldering. Be very careful to whom you entrust this work as most ‘welding shops’ are unlikely to be up to the task. You’ll need a real craftsperson here. You might begin by asking a custom jeweler for recommendations.
Even though the welds were originally resistance welds (‘spot-welds’), don’t let anyone try to persuade you to let them ‘re-weld’ the old ones. I’ve never seen that done successfully. When properly executed, silver soldering should produce a very strong, neat and tidy connection.
Broken Wires – This is by far the most challenging of repairs and there is no set procedure. If a wire is broken, the surrounding area is very often distorted so you’ll need someone who is not only a very good welder or solderer but also has a keen eye for form. End-to-end wire repairs may be best carefully TIG or gas welded. Listen to the opinion of the repair person carefully before making a judgement.
In most cases, the cost of repair – refinishing the basket and base and repairing some broken welds is worth it and can give your chair a new lease on life. If your chair requires major surgery – broken wires, mangled geometry, etc., it may not be worth the cost. Start with the assessment and cleaning and the rest should become clear. Thank you for preserving a piece of the past.
Additional Care & Repair Tips
How to best care for your piece depends on the condition it is in.
Dust & Grime
Unless you have a fragile or delicate piece, gently washing the sculpture will not harm it. Take it outside, turn on your spray hose and rinse it down. Immediately dry the metal thoroughly and completely with a clean cloth. If it is still not clean to your satisfaction, take a dab of mild dish soap (such as Ivory Liquid) and mix with warm water. With an old toothbrush or other soft-bristle brush, lightly scrub your sculpture. Rinse with plain water and dry immediately. Most metal sculptures are fairly robust. Unless you use intense chemicals, you probably won’t hurt it.
Discoloration, Rust, White Spots
The foundation recommends the cleaning product CLR (Calcium, Lime, Rust) to remove light spots. Follow the instructions on the container. Do not let it sit on the surface for too long as it may begin to eat away at the metal or the patina. Do not use sandpaper or a metal brush – it is too rough and will destroy the surface of the metal. If your sculpture has acquired the green patina of weathered copper or bronze, applying CLR as directed should remove it, if desired.
Non-Patinated Metal
If you have a sounding sculpture that was once shiny and bright but has darkened considerably, you may wish to shine it up again. If you plan to sell it, place it in an exhibition, or display it publicly in the near future, we recommend that you check with your auctioneer or museum director before polishing. The metal polish MAAS (available at MAASinc.com) has worked well for us. Follow the package directions. Make sure you get all the polish off and rub with a soft, clean cloth.
Centennial Table Tonal
These limited edition sculptures are not patinated and can be polished as desired, as specified above for non-patinated metal. If your piece has collected dust or pet hair between the rods, take a strip of cloth or Q-tip and slide it back and forth until the dust is removed.
Bent Rod
If a rod of a tonal has accidentally been bent out of place, disrupting the orderly placement, you can attempt to bend it back with patience and gentleness. Carefully pull the out-of-place rod(s) in the opposite direction, slightly past the desired original location, until it stays in the right spot. Make sure you don’t mistakenly include a previously straight rod, and do it in small increments. If the rods are too damaged you will need to have a professional repair it.
Professional Repairs
If your art is badly damaged or in need of serious conservation, there is hope. Look for capable metalsmiths or art conservators in your area, or contact the following experienced Bertoia repair sources:
- Flatlander Sculpture in Michigan (FlatlanderSculpture.com)
- Modern Art Conservation in New York (ModernArtConservation.com)
We have found good results working with both companies.
Protection
If desired, microcrystalline Renaissance Wax may be added as a protective coating. Many museums use it. The wax does not collect dust, protects your piece, and also prevents age patination.
Chances are extremely low that you found a prototype. There were only a handful and most are in museums or collectors’ homes. You can contact Bill Shea, our chair expert, if you are convinced you have something special. billshea356@gmail.com
As for any original design/art/invention, you are doing several positive actions by purchasing the authentic item.
You are
1) honoring the original designer and conceptually, all designers,
2) getting a quality product that will hold its value,
3) obtaining the product as the designer envisioned and not an uncomfortable imitation and
4) you are tapping into a small slice of that inventor’s creative spirit. By purchasing a cheap imitation, you will get an initial lower cost but may be disappointed with the lack of ergonomics, quality and durability.
If you send photos, dimensions and anything else you know about it, we will be happy to take a quick look at no charge. We do NOT authenticate anything but you can submit your piece to the Catalogue Raisonné.
We do NOT issue authentications, but you can submit to the Catalogue Raisonné and, if approved, get a CR number. Entries require the art data form, the release form, photos, and payment. Sculpture administration fee is $500, and works on paper fee is $250. See all details under the catalogue raisonné category.
If you are curious what your piece might sell for, a casual opinion should suffice. Send an email with photo, dimensions, and history of ownership. If you are getting art insurance or involved in the 4 D’s (divorce, death, donation, distribution) you will need a full appraisal report. This is a lengthy process that may cost $1000 or more by our ASA appraiser. We do NOT issue authentications but you may want to submit to the Catalogue Raisonné (see above). If you are still confused, email us.
Yes. Celia Bertoia is a member of the Appraisal Society of America and is very familiar with her father’s work (and other modern art). She has researched Bertoia collections for individuals and companies for various purposes, i.e. insurance, charitable donation, estate, divorce, or whatever your specific need is. She has also acted as an expert witness in court. Unless your artwork is very unusual or in questionable condition, she probably can inspect via Zoom or high resolution photos to avoid shipping. Celia is in southern Utah, 100 miles from Las Vegas. Send your query to info@harrybertoia.org.
The “spray” type sculptures have become problematic in recent years. There are many spray copies and would-be Bertoias out there that are not original Harry Bertoia pieces. If you or your relative/associate acquired it directly from Harry or one of his gallery representatives and you have documentation, the answer is probably yes. If you came by it through second-hand means with no documenting paperwork, it may be a challenge. You can submit to the CR, but it may or may not be approved for entry. We cannot give a CR# to a spray sculpture that does not have substantiating evidence regarding the artist. Read more.
Simply go to the CR website, search here. If it’s not currently in the CR, you can submit here along with photos, provenance, dimensions and any unusual details. We review 4 times per year, and there is a charge.
Very possibly! Tell us what you have of value and what you want and perhaps we can trade. If you qualify, we can offer a 10% discount to non-profits. If you want to work here, again, tell us about yourself and we’ll be happy to talk. Here is a form to start with.
We need your submission by April 1 of any year. We offer an art scholarship of $1000 to one man and one woman going to an accredited school. We are partial to Utah students. Requirements are on the form.
Yes, please! We are a non-profit 501 (c)(3) and it may be a deduction according to your tax expert. Here are samples of what your money will do for us:
$50 allows us to keep in touch with you for one day on social media.
$100 buys snacks and drinks for an open house.
$500 pays for one wooden crate in which to ship a sculpture to shows or galleries.
$1000 pays for one entry of the Catalogue Raisonné research and formatting.
$5000 will make us laugh and cry and then upgrade our office equipment.
LARGE SUMS for a Sonambient barn collection building, creating a sounding sculpture app for the public to play their own concert, or conserving stained damaged sculptures are definitely welcome. Let’s talk.
Yes, of course, you can include us in your will or trust. Give us a call. Donate here.
If you need photos of chairs, MillerKnoll, Inc. owns all rights to the chairs. Contact them at https://www.millerknoll.com/
For images of Harry or his art, let us know exactly what you are looking for. We may have it here. You can also check at our sister organization in Italy, ArietoBertoia.com. If you still can’t find what you want, we may have lo-res photos of your topic. Contact us at info@harrybertoia.org
If you are working on a scholarly paper or a non profit newsletter or something similar, there is no charge, but please inform us of your project and the photos used at info@harrybertoia.org. If you have a larger project in mind, please contact Artist’s Rights Society at info@arsny.com or visit arsny.com for permission and licensing.
We use Artists Rights Society for legal purposes.
Please contact Artists Rights Society in New York:
Generic: info2@arsny.com
212 420-9160
We do not act as dealers, as it is a conflict of interest. That said, if you are looking for something specific, you might ask as we occasionally hear of available objects. Email: info@harrybertoia.org.
Original monotypes (works on paper) from the estate are handled by Hosfelt Gallery in San Francisco. Ask for Todd Hosfelt.
Note that http://www.bertoiaauctions.com sells antique toys, NOT Bertoia artwork.
A list of auction houses that normally handle Bertoia can be found here. Other galleries that often have Bertoias can be found here.
Let us know exactly what you are looking for and we will access what you need and get it to you. The more specific you can be with dates, names, and details, the better the results will be. We are currently working on making some archival material publicly accessible, but we’re not there yet.
A round coffee table, published in one German Knoll catalogue in 1952, model 401, as a Harry Bertoia design, as far as we can discern, is NOT a Bertoia design. We have checked with numerous older knowledgeable Knoll employees who tell us that there was never a Bertoia table. Celia Bertoia, daughter, states that “We had all the Bertoia furniture in the house – chairs, benches, ottoman – but we NEVER had a table.
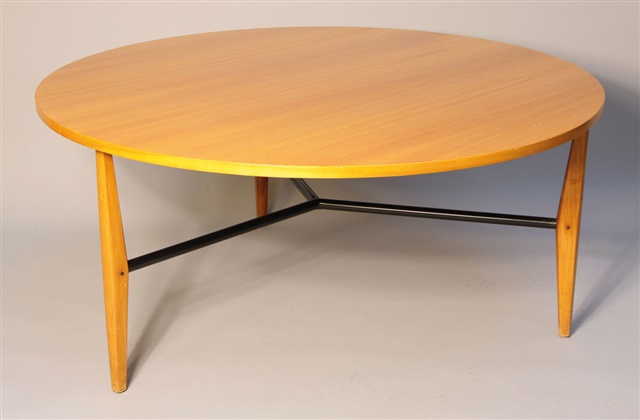
This is NOT a Bertoia design