Catalogue Raisonné Update – May 2019
We previously announced that the Foundation has started the monumental task of producing a Catalogue Raisonné. Most organizations that undertake the total documentation of an artist’s body of work have to contend with a few thousand pieces of art. A catalogue of 8,000, for example, is considered huge. While we don’t know for sure, the estimate of Bertoia’s works is in the area of 15,000+. We also made the decision to approach the project comprehensively, meaning that instead of focusing on one aspect of Bertoia’s practice, the Catalogue Raisonné will include his: monotypes, paintings, drawings, jewelry, flatware, hollowware, furniture designs and prototypes, and 9 different categories of sculptures including the large-scale commissions!
Understanding the daunting task facing us should give you a great appreciation for our Harry Bertoia Catalogue Raisonné Project Director.
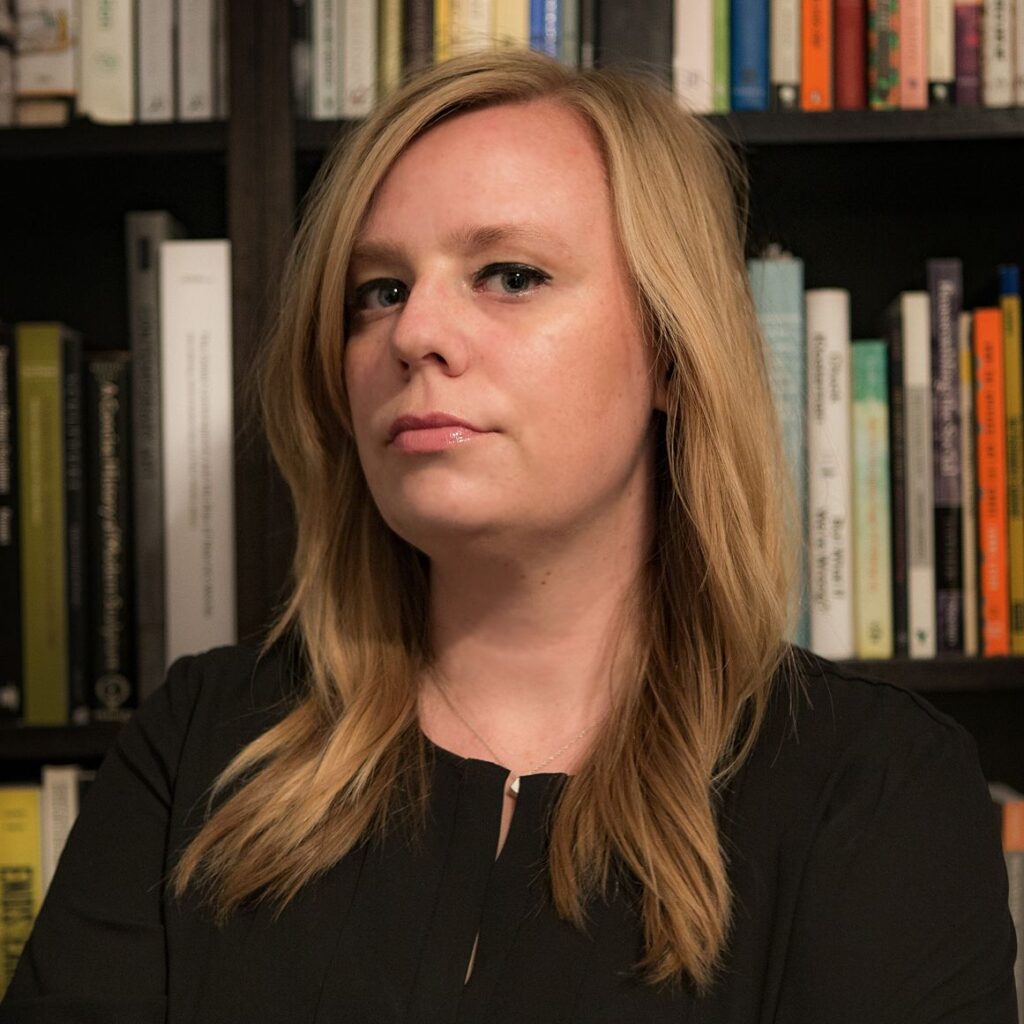
May I introduce Dr. Marin R. Sullivan? She is a Chicago-based art historian and curator, and has a Ph.D. in History of Art from the University of Michigan. Her area of specialization is the history of modern and contemporary sculpture, especially as it relates to architecture and design, and she has authored numerous articles and books related. Marin lectures, teaches, obtains grants, curates, coordinates, researches, and… basically does it all! See her specifics at: SculpturalThings.com
This was when we were still located in Montana, and I knew that they were serious when they came in person to visit the Foundation in Bozeman. Traveling to Bozeman requires strong desire and fortitude! Upon meeting Marin, I immediately enjoyed who she was.
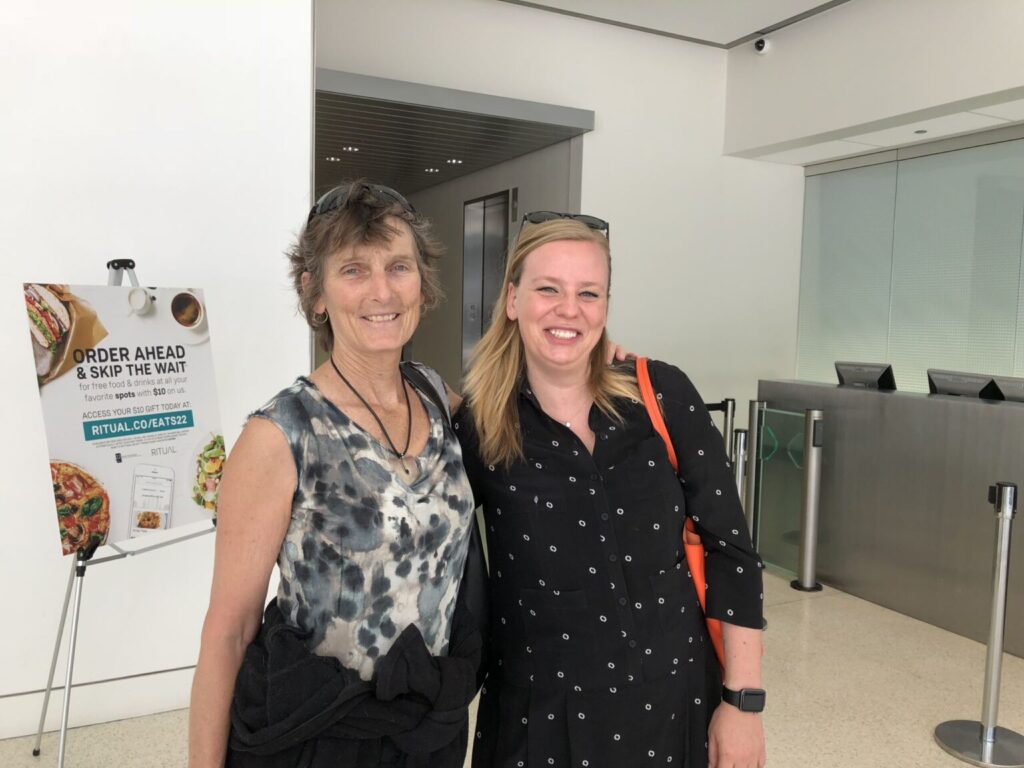
Marin and I first met because of her passion for Harry Bertoia. She sought archival documents for Bertoia articles and lectures that she was working on. As we chatted and emailed, I could tell she was crazy about Bertoia. Our next encounter occurred when she and Jed Morse, Chief Curator at the Nasher Sculpture Center, approached the Foundation about a retrospective Bertoia exhibition, which is now scheduled to open in Dallas in September 2020.
We had the opportunity to mingle again in Chicago, her hometown, when my first impression was reinforced. She is highly professional while managing to be friendly and approachable at the same time; a remarkable combination.
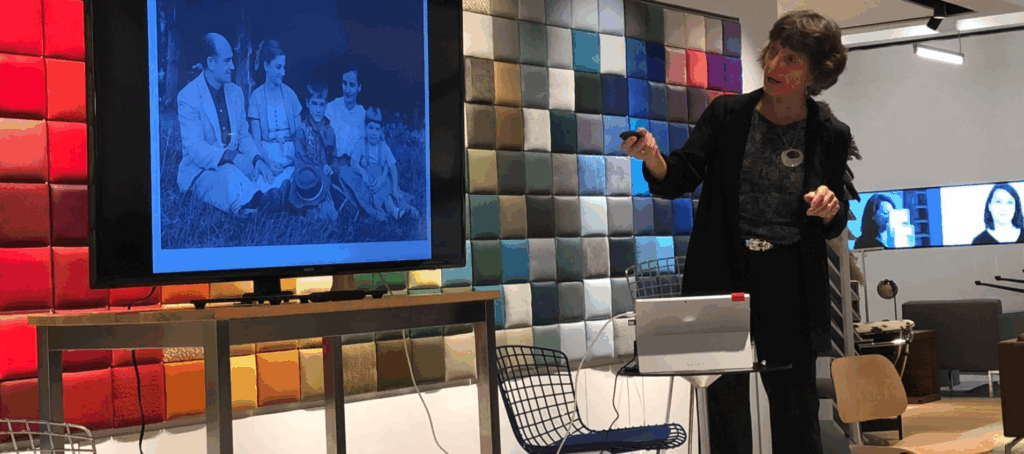
UPHOLSTERY
This is the easy one. Different upholstery options were offered at any given time – typically: no upholstery, a simple seat pad, two-piece seat and back pads and fully upholstered. Also different fabrics and upholstery details have been offered over the years. But, the good news is that replacement upholstery cushions are very much available directly from Knoll and lower priced knock-off replacements are available online. Knock-off quality varies so be careful… you get what you pay for. Note from Celia: I’ve had local upholstery shops do a very good job on full upholstery with cost dependent on fabric; talk to your local shops. A Diamond, Bird and Ottoman total came to $500 here in St George, Utah.
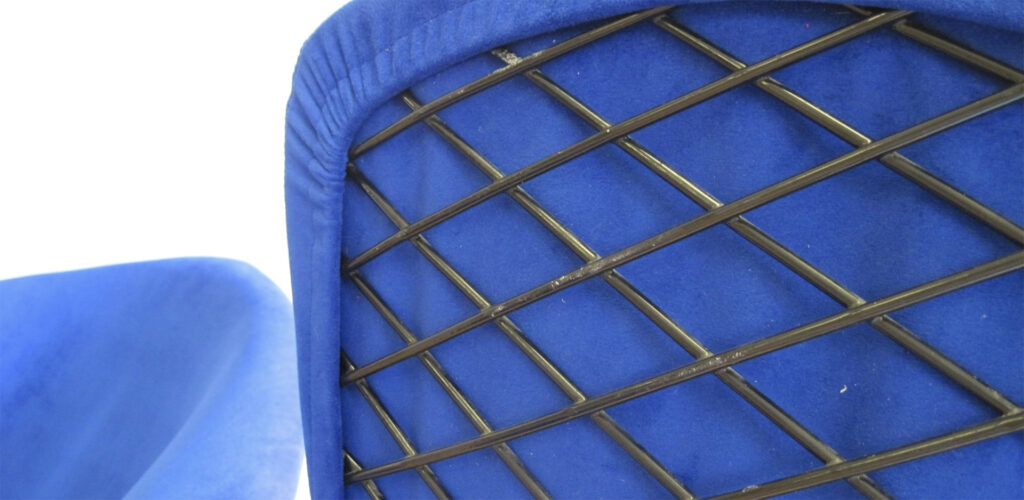
FINISH
During its production history, the finish has changed many times and perhaps the most difficult task in refurbishing the finish is determining what the finish is! Many have been used over the years and the ‘technical descriptions’ in the price lists can be vague, confusing or downright wrong.
Early chairs made from 1953 – 1976 were only available in black, white and chrome or black and white two-tone (chrome was added in 1956). The black was a simple black oxide finish and was used through the mid ‘60s (this is the same finish used for black nuts and bolts found in the hardware store). This proved to not be a very durable finish and prone to rust so later ones were also dipped in cosmolene and wiped off. In the early ‘70s the catalog description was changed to ‘black epoxy’ which I presume was powder-coated.
White – White was described in a head-spinning number of ways from white vinyl, lacquer, white fused, white epoxy and Rilsan (nylon). The different finishes were applied in various ways but the most common one was (and is still used to this day) is applied by a process known as ‘Fluidized Bed’. This produces a very heavy build, perfect finish and was/is used for epoxy and Rilsan (nylon). It’s interesting to note that the Rilsan (nylon) powder which was developed in Italy in the early ‘40s is derived entirely from castor beans and therefore a ‘green’ material. It’s also the most common finish found on white Bertoia chairs.
Colors – Red, yellow, green, blue, brown (plus white and black) polyester or epoxy powders were added to the scope in the 77/78 price list. These were applied by powder-coating.
Plated – Polished chrome has been a standard option since 1956. Satin chrome and gold-plated finishes have been added in recent years.
Though its not clear if any were shipped to customers, one still finds chairs with a white very gloppy, saggy (frankly, ugly) finish usually referred to as the ‘dish drainer’ finish which is just that: the dip-molded finish used on Rubbermaid dish drainers.
By now you’re probably scratching your head wondering what kind of finish is on your white chair. The good news is that it really doesn’t matter… regardless of color. Let’s take a close look at your chair and determine the best corrective action.
Cleaning – It’s about time. If you hadn’t bathed in decades, you’d need a good cleaning, too. Begin with a bucket of hot water and dishwashing liquid (I recommend Dawn detergent) and a medium-stiff dishwashing brush. If that’s not sufficient, move up to dishwasher liquid which is more alkaline. Rinse well and allow to dry thoroughly.
Minor Dings – Chips, scratches and scrapes can usually be touched-up with reasonable success. Begin by scraping or sanding to remove rust. Be sure to keep the sanded area small and blend to a feather edge with the surface of the paint. Clean with alcohol and you’re ready.
Some recommend the use of product called ReRack or Uber Goop, available online or at many hardware stores. This is intended for the repair of dishwasher racks and is only available in white or gray color. Even shaken, it’s lumpy and difficult to apply neatly. The resulting patch is much too soft and rubbery to my liking. I don’t recommend it.
I find a much better alternative to be automotive touch-up paint such as Dupli-Color Scratch Fix. It has an applicator pen and brush and is easy to apply. Don’t forget that it shrinks quite a bit when dry, so it may need two coats. Also, be careful in the color selection as there are a number of whites to choose from and some will match your chair better than others.
Major Issues – Rust, flaking, chipping and peeling are not uncommon, especially on chairs that have been used outdoors for extended periods of time. This requires fully stripping and refinishing. Also, if you find structural issues such as broken wires, failed welds et cetera, stripping is a must.
The stripping process is complicated and chemical strippers rarely work. Usually the finish is baked off in a large oven at around 700 degrees F and then lightly sandblasted. Finally, the base and basket are repainted using either the powder-coat or fluidized bed method. Because powder-coaters are to be found nearly anywhere whereas fluidized bed contractors are few and far between, powder-coaters are probably your only practical choice. A good powder-coater should have numerous powder options: colors, gloss level, high-build, UV-stabilized and so on. Some are more appropriate than others so you should discuss which is the best choice for your application. The good news is that most powder-coaters offer one stop shopping: stripping, bead-blasting and painting in-house. The cost should be around $100 – $125.
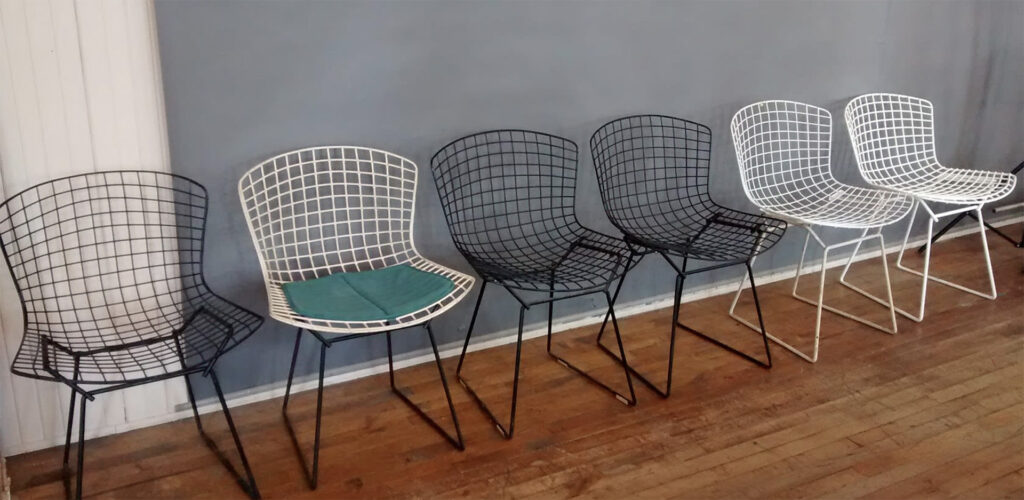
STRUCTURAL REPAIR
Anything can break but not everything can be repaired. Fortunately, Bertoia chairs usually can be. Just keep in mind that all repairs require that the chair be stripped first.
Broken Welds – The most common structural problem is broken welds, especially on chairs made in the early ‘50s. Keep in mind that all Bertoia production chairs were welded (more accurately, resistance welded) as opposed to brazed, hard soldered etc. but repairs are best made by brazing, or better yet, silver soldering. Be very careful to whom you entrust this work as most ‘welding shops’ are unlikely to be up to the task. You’ll need a real craftsperson here. You might begin by asking a custom jeweler for recommendations.
Even though the welds were originally resistance welds (‘spot-welds’), don’t let anyone try to persuade you to let them ‘re-weld’ the old ones. I’ve never seen that done successfully. When properly executed, silver soldering should produce a very strong, neat and tidy connection.
Broken Wires – This is by far the most challenging of repairs and there is no set procedure. If a wire is broken, the surrounding area is very often distorted so you’ll need someone who is not only a very good welder or solderer but also has a keen eye for form. End-to-end wire repairs may be best carefully TIG or gas welded. Listen to the opinion of the repair person carefully before making a judgement.
In most cases, the cost of repair – refinishing the basket and base and repairing some broken welds is worth it and can give your chair a new lease on life. If your chair requires major surgery – broken wires, mangled geometry, etc., it may not be worth the cost. Start with the assessment and cleaning and the rest should become clear. Thank you for preserving a piece of the past.
Additional Care & Repair Tips
How to best care for your piece depends on the condition it is in. Click on any of the sections below to learn more.
Dust & Grime
Unless you have a fragile or delicate piece, gently washing the sculpture will not harm it. Take it outside, turn on your spray hose and rinse it down. Immediately dry the metal thoroughly and completely with a clean cloth. If it is still not clean to your satisfaction, take a dab of mild dish soap (such as Ivory Liquid) and mix with warm water. With an old toothbrush or other soft-bristle brush, lightly scrub your sculpture. Rinse with plain water and dry immediately. Most metal sculptures are fairly robust. Unless you use intense chemicals, you probably won’t hurt it.
Discoloration, Rust, White Spots
The foundation recommends the cleaning product CLR (Calcium, Lime, Rust) to remove light spots. Follow the instructions on the container. Do not let it sit on the surface for too long as it may begin to eat away at the metal or the patina. Do not use sandpaper or a metal brush – it is too rough and will destroy the surface of the metal. If your sculpture has acquired the green patina of weathered copper or bronze, applying CLR as directed should remove it, if desired.
Non-Patinated Metal
If you have a sounding sculpture that was once shiny and bright but has darkened considerably, you may wish to shine it up again. If you plan to sell it, place it in an exhibition, or display it publicly in the near future, we recommend that you check with your auctioneer or museum director before polishing. The metal polish MAAS (available at MAASinc.com) has worked well for us. Follow the package directions. Make sure you get all the polish off and rub with a soft, clean cloth.
Centennial Table Tonal
These limited edition sculptures are not patinated and can be polished as desired, as specified above for non-patinated metal. If your piece has collected dust or pet hair between the rods, take a strip of cloth or Q-tip and slide it back and forth until the dust is removed.
Bent Rod
If a rod of a tonal has accidentally been bent out of place, disrupting the orderly placement, you can attempt to bend it back with patience and gentleness. Carefully pull the out-of-place rod(s) in the opposite direction, slightly past the desired original location, until it stays in the right spot. Make sure you don’t mistakenly include a previously straight rod, and do it in small increments. If the rods are too damaged you will need to have a professional repair it.
Professional Repairs
If your art is badly damaged or in need of serious conservation, there is hope. Look for capable metalsmiths or art conservators in your area, or contact the following experienced Bertoia repair sources:
- Flatlander Sculpture in Michigan (FlatlanderSculpture.com)
- Modern Art Conservation in New York (ModernArtConservation.com)
We have found good results working with both companies.
Protection
If desired, microcrystalline Renaissance Wax may be added as a protective coating. Many museums use it. The wax does not collect dust, protects your piece, and also prevents age patination.